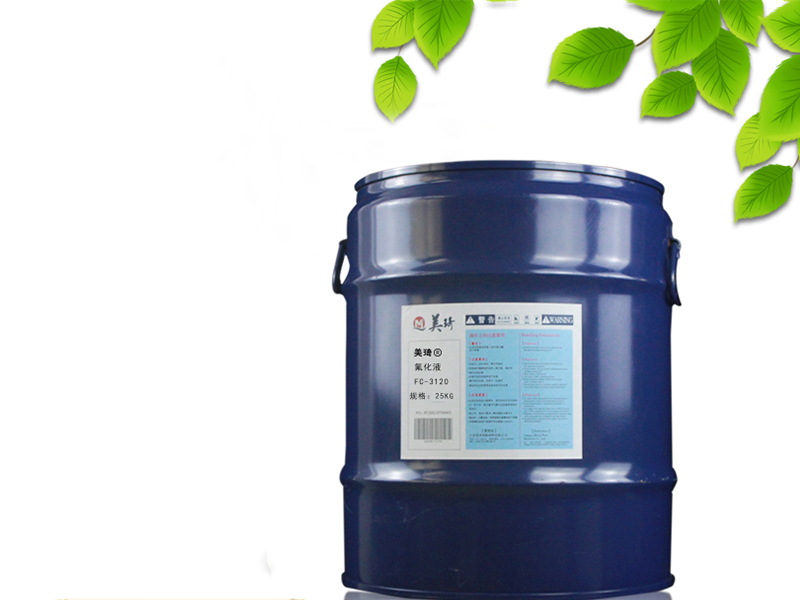
FC-40电子氟化液:在智能制造中的应用与挑战
- 江西美琦
FC-40电子氟化液:在智能制造中的应用与挑战
在智能制造的浪潮中,算力需求与设备散热的矛盾日益凸显。以AI服务器集群为例,单GPU芯片功耗突破700瓦,机柜功率密度攀升至50kW/柜,传统风冷技术已无法满足散热需求。FC-40电子氟化液凭借其独特的物理化学特性,成为解决这一矛盾的关键材料。然而,其规模化应用仍面临技术标准、成本控制与环保替代等多重挑战。
一、FC-40的核心特性:智能制造的“散热引擎”
FC-40是一种全氟化电子氟化液,其分子结构中C-F键键能高达485kJ/mol,赋予其卓越的化学惰性与热稳定性。其液程范围为-57℃至165℃,沸程狭窄(150-200℃),可确保在连续运行中成分稳定性。该材料具有以下特性:
超高热传导效率:在单相浸没式液冷系统中,FC-40的导热系数达0.06W/(m·K),较空气提升3000倍,可实现40-55℃高温供液,支持全年自然冷却。
材料兼容性:与半导体封装材料(如环氧树脂、硅胶)的接触角小于15°,无腐蚀性,兼容超过200种电子元器件,确保清洗后无需二次处理。
安全环保性:不可燃、无残留,臭氧消耗潜值(ODP)为0,全球变暖潜值(GWP)低于150,符合欧盟REACH法规。
二、智能制造场景中的突破性应用
1. 数据中心液冷革命
在微软Azure昆西数据中心,FC-40用于双相浸没式冷却系统,使服务器功耗降低5%-15%。某超算中心采用该技术后,PUE值从1.6降至1.12,年节电量达2.3亿千瓦时。其优势在于:
能效提升:通过直接接触散热,消除芯片与冷却介质间的热阻,使CPU温度降低20-30℃;
空间优化:单台机柜功率密度从30kW提升至200kW,占地面积减少75%;
运维简化:冷却系统故障率下降90%,维护周期延长至5年。
2. 半导体制造的“隐形守护者”
在晶圆制造中,FC-40被用于光刻胶显影后的清洗环节,其表面张力仅12mN/m,可渗透至0.13μm线宽的沟槽结构,清洗效率较传统IPA提升40%。在刻蚀工艺中,作为控温介质,其热容达1.1J/(g·K),确保晶圆表面温度波动小于±0.5℃。
3. 新能源汽车的“温度管家”
在特斯拉4680电池包中,FC-40用于浸没式电池热管理系统,使快充温度上升速率降低60%,循环寿命延长30%。在800V高压平台电机控制器中,其击穿电压达60kV/mm,确保绝缘可靠性。
三、规模化应用的三大挑战
1. 技术标准缺失
目前,国内尚无针对FC-40的专项国家标准,行业测试方法分散。例如,在生物毒性测试中,部分企业采用鱼类急性毒性试验(LC50>1000mg/L),而国际标准要求慢性毒性(NOEC)测试。这导致不同企业的产品兼容性认证周期长达18个月,增加应用成本。
2. 成本与供应链压力
FC-40市场价格约为20万元/吨,单台40kW机柜需用量约500L,初期投资成本高昂。2024年进口依存度仍达45%。3M计划于2025年底停产相关产品,加剧供应链风险。
3. 环保替代需求
欧盟《PFAS限制提案》要求2030年前淘汰PFAS类氟化液,而FC-40的降解半衰期长达5年。当前,氢氟醚类(如HFE-7100)虽GWP<5,但沸点仅61℃,无法满足高温场景需求。国内企业正在研发的“短链全氟化物”技术,其降解产物毒性降低90%,但热稳定性尚未达标。
四、未来展望:技术突破与产业协同
面对挑战,行业正从三个维度寻求突破:
标准建设:全国团体标准信息平台已立项《电子氟化液生物毒性安全技术规范》,预计2026年发布;
生态构建:中芯国际与永和股份共建“氟化液应用实验室”,开发晶圆级清洗-冷却一体化工艺,目标将单位产能能耗降低35%。
在智能制造的“双碳”目标下,FC-40电子氟化液既是过渡期的关键技术,也是产业升级的催化剂。随着材料科学、制造工艺与标准体系的协同演进,其应用边界将持续拓展,为高端制造注入“液冷动能”。